Delivers driving force with robust structure for efficient belt operation.
Overview
Drive pulley is a key component in belt conveyor systems, working in conjunction with the motor to provide the traction force needed for continuous material transport.
It is widely used in heavy-duty applications such as mining, power, ports, cement, and metallurgy.
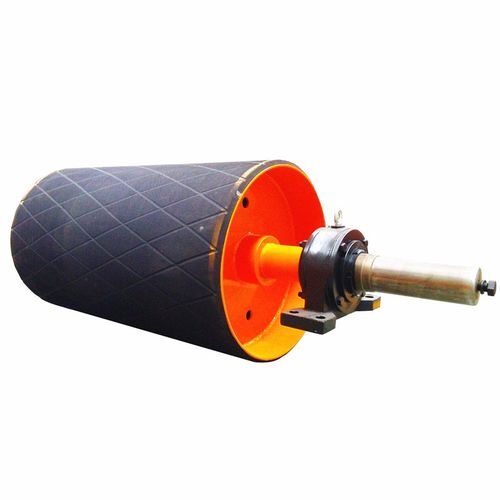
More Details For Our Customers
Structure Composition
A drive pulley typically consists of the drum shell, main shaft, bearing housings, bearings, sealing system, and hub structure. Optional features include welded or crowned designs, with rubber lagging (cold-bonded or hot-vulcanized) to enhance grip.
Custom Options & Parameters
·Drive pulleys are the key power transmission components in conveyor systems and can be tailored in many aspects depending on site requirements. Main configurable options include:
·Pulley Diameter & Length: Common diameters range from φ220 to 1250mm. Lengths are customized based on belt width and system power needs (e.g., 500mm, 1000mm, 1600mm).
·Shaft & Bearing Housing: Available shaft sizes include φ50, φ60, φ80, φ100mm with matching housings such as SN or SD series.
·Lagging Type & Thickness: Options include plain or diamond/chevron patterned lagging, with rubber thickness typically 8–20mm, made of standard, wear-resistant, or ceramic materials.
·Shaft End Connection: Various designs supported such as single or double drive, with keyway, locking bush, or flange-type coupling.
·Balance Level & Testing: Optional dynamic balancing (e.g., G40, G16) available to suit high-speed or heavy-duty applications.
Manufacturing & Quality Control
Our drive pulleys are built using high-strength welded structures and precision machining, ensuring reliable performance under heavy-duty and harsh conditions:
·Durable Structural Materials: Drums are fabricated from thick welded pipes or steel plates, with tempered alloy steel shafts for enhanced strength and fatigue resistance.
·Advanced Machining: CNC turning ensures precise fit between pulley shells and bearing housings, supporting long-term alignment and balance.
·Dynamic Balancing: All drive pulleys are dynamically balanced to ensure low vibration and noise at high speeds.
·Reliable Lagging Process: Various lagging methods available, such as hot vulcanization and cold bonding, ensure strong adhesion and high wear resistance.
·Strict QC Process: Quality control includes weld inspection, dimensional checks, load testing, visual inspection, and balance verification before delivery.
FAQ or Maintenance Tips
·FAQ
Slippage or belt pulling often occurs due to worn lagging or insufficient tension.
·Maintenance Tip
Check lagging wear regularly, adjust tension, or replace lagging as needed.
Note:
We support customized drawings, sample development, small-batch prototyping, and mass production to meet diverse product requirements under complex working conditions in industries such as mining, cement, steel, power, and ports.
Product Features
Stable Power Transmission
Robust design ensures reliable power delivery under high load and frequent operation.
Lagging for Better Traction
Lagging increases friction with the belt, prevents slippage, and extends belt life.
Versatile Structural Options
Available in straight or crowned types with flexible bearing configurations.
Durable & Easy Maintenance
High-strength materials and sealed design reduce downtime and extend service life.
Need a custom solution?
Let’s make it simple.
Professional OEM/ODM services to match. From function to design, we offer fast and flexible customization to meet your exact needs.
Customization Options
Size Flexibility
Roller length, pulley diameter, shaft size, and other dimensions can be precisely tailored to fit specific conveyor systems.
Material Selection
Various materials including carbon steel, stainless steel, aluminum, and polymers are available for different environments.
Surface Finish
Powder coating, zinc plating, hot-dip galvanizing, and rubber lagging enhance corrosion resistance and surface grip.
04.
Sealing Design
Optional sealing systems such as labyrinth seals, steel cap seals, and fully enclosed designs improve dust and water protection.
05.
Rubber Ring Type
Impact idlers support various rubber ring types and hardness levels, effectively handling different shock loads and operational conditions.
06.
Engineering Support
We support custom development based on drawings or samples, and assist in structure optimization and non-standard design.
Applications Across Industries

Mining
Tear-resistant steel cord belts withstand continuous impact from sharp-edged ores
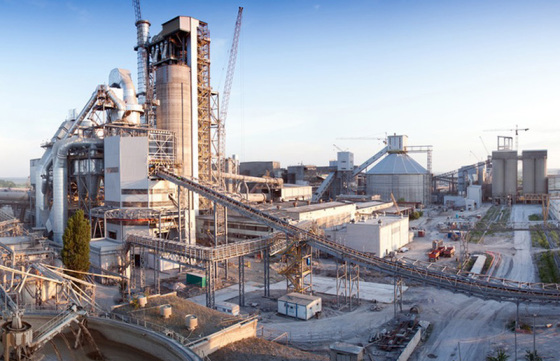
Cement Plants
Heat-resistant covers (+150℃) prevent surface carbonization during clinker conveying.
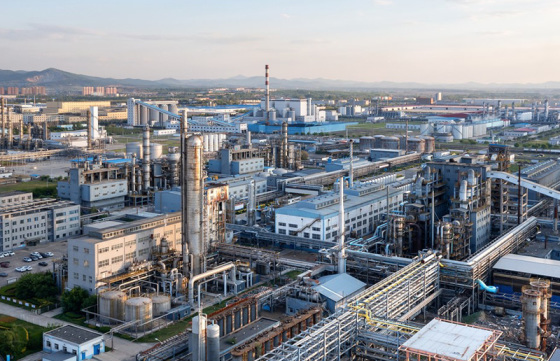
Chemical Industry
Transports fertilizers/plastic pellets using corrosion-proof rubber & enclosed structures.
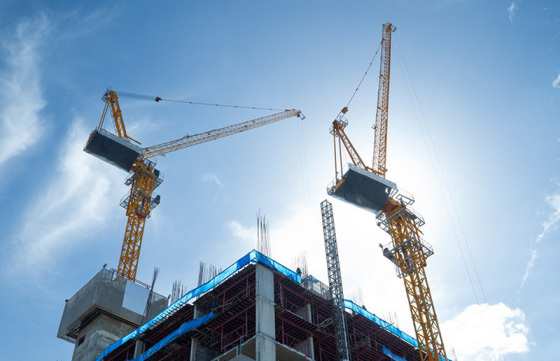
Construction
Wide belts for sand/concrete with high-capacity design.
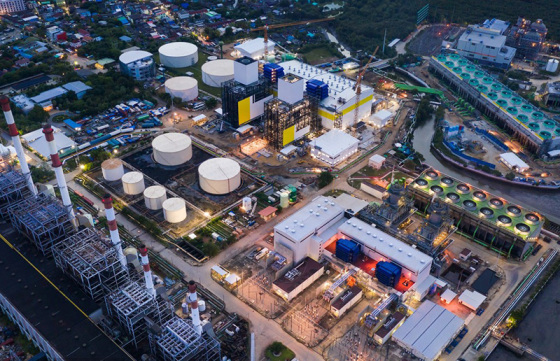
Power Plants
Anti-static guide strips eliminate spark risks in coal conveying.
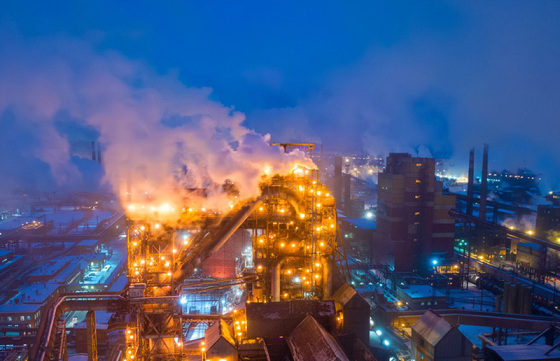
Steel Mills
Handles iron ore/slag at 800°C with alloy-reinforced carcass.
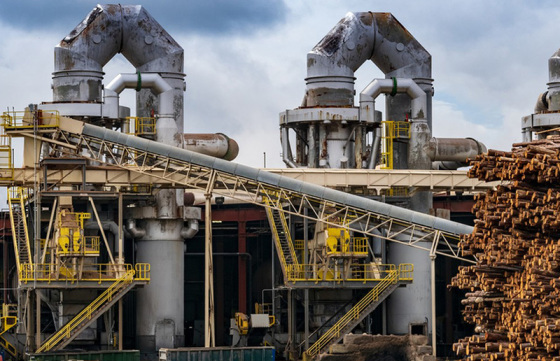
Logging
Reinforced belts transport logs/sawdust with puncture-proof layers.
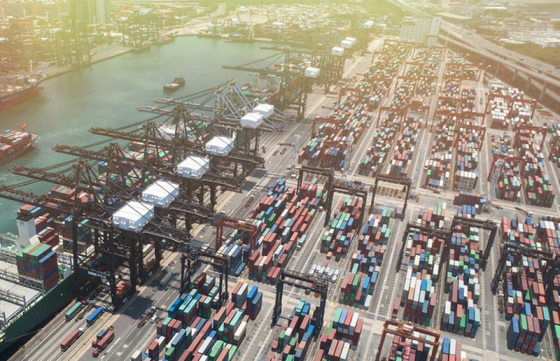
Logistics
Anti-salt spray rubber compound extends service life in humid port operations.
Reach Out Today
Contact us to get a free quote, your project will meet a right solution with us.
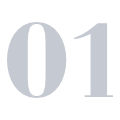
Tell Us What You Need
Tell us as specific as possible of your needs, provide the drawing, reference picture and share your idea to us.
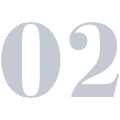
Get Solution & Quote
We will work on the best solution according to your requirements, and quote will be provided within 24 hours.
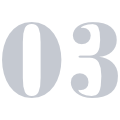
Approve Mass Production
We will start mass production after approval and deposit, and we will handle the shipment and future after-sale service.